Proteção de máquinas e equipamentos: Melhores práticas para garantir a segurança
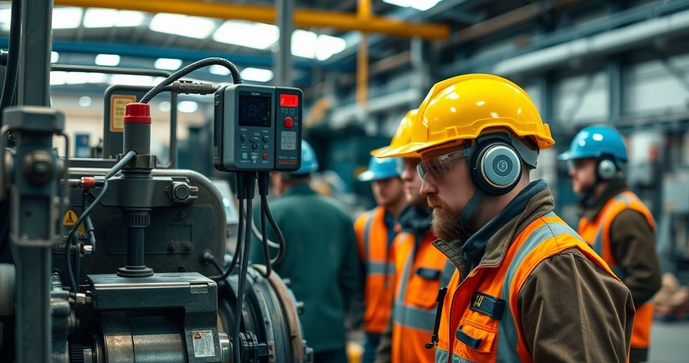
Por: Ingrid - 26 de Abril de 2025
A proteção de máquinas e equipamentos é fundamental para evitar acidentes e garantir a segurança dos colaboradores nas indústrias. Com o aumento da automação e a complexidade dos sistemas mecânicos, torna-se imprescindível implementar medidas eficazes que assegurem tanto a integridade dos operadores quanto a funcionalidade dos equipamentos. Este guia apresenta as melhores práticas e normas que devem ser seguidas para criar um ambiente de trabalho seguro.
Importância da proteção de máquinas no ambiente industrial
A proteção de máquinas é um aspecto crítico no ambiente industrial, pois garante não apenas a segurança dos colaboradores, mas também a eficiência operacional. A implementação de medidas adequadas de proteção reduz significativamente o risco de acidentes de trabalho, que podem resultar em lesões físicas e até mesmo fatalidades.
Além de proteger os trabalhadores, a segurança das máquinas é essencial para a continuidade do processo produtivo. Equipamentos danificados ou que falham em operação podem causar paradas inesperadas, resultando em perda de produtividade e aumento de custos operacionais. Investir em proteção adequada ajuda a minimizar esses riscos, garantindo que as máquinas funcionem conforme esperado.
A conscientização sobre a importância da proteção de máquinas também contribui para a cultura de segurança dentro da empresa. Quando os colaboradores entendem os riscos envolvidos e as medidas de proteção em vigor, eles tendem a agir de maneira mais cautelosa e responsável, promovendo um ambiente de trabalho mais seguro.
Além disso, o cumprimento das normas de segurança estabelecidas por órgãos reguladores, como a NR-12, é fundamental. Essa norma estabelece requisitos mínimos para a prevenção de acidentes e é um pilar na proteção de máquinas e equipamentos. Negligenciar a segurança pode levar a penalidades legais e danos à reputação da empresa.
Por fim, as empresas que priorizam a proteção de máquinas e equipamentos não apenas salvaguardam a vida dos trabalhadores, mas também fortalecem sua imagem no mercado. Organizações comprometidas com a segurança são geralmente mais valorizadas pelos seus clientes e parceiros, abrindo portas para novas oportunidades de negócios.
Principais normas de segurança para máquinas e equipamentos
As principais normas de segurança que regem a proteção de máquinas e equipamentos são fundamentais para garantir um ambiente de trabalho seguro. No Brasil, a Norma Regulamentadora NR-12 é uma das mais importantes, pois estabelece requisitos mínimos para a segurança no trabalho com máquinas e equipamentos, visando à prevenção de acidentes.
A NR-12 aborda aspectos como a instalação, operação, manutenção e desativação de máquinas, garantindo que os equipamentos sejam projetados e mantidos para operar de forma segura. Entre os pontos principais estão a necessidade de dispositivos de segurança, sinalização adequada e a qualificação dos operadores.
Outra norma relevante é a NR-10, que se concentra na segurança em instalações e serviços em eletricidade. Esta norma é crucial para máquinas que utilizam energia elétrica, estabelecendo medidas de proteção contra choques elétricos e garantindo que os operadores estejam devidamente capacitados.
A NR-26 trata da sinalização de segurança, exigindo que as instalações industriais possuam advertências visuais que informem sobre os riscos presentes no ambiente de trabalho. Essa sinalização não apenas orienta os colaboradores, mas também ajuda na prevenção de acidentes, ao deixar claro quais cuidados devem ser tomados.
Além das normativas nacionais, é importante considerar normas internacionais, como as da ISO (Organização Internacional de Normalização) que promovem boas práticas em segurança industrial. Normas como a ISO 12100 estabelecem diretrizes sobre o design seguro de máquinas e equipamentos, sendo referências valiosas para empresas que buscam se alinhar com padrões globais.
O cumprimento criterioso dessas normas não só representa uma obrigação legal, mas também é um investimento na segurança e na saúde dos colaboradores. Empresas que seguem as regulamentações pertinentes demonstram um compromisso com a proteção de seus profissionais e com a continuidade segura de suas operações.
Soluções de proteção: dispositivos de segurança e sinalização
Implementar soluções de proteção adequadas é fundamental para garantir a segurança dos colaboradores que operam máquinas e equipamentos. Entre as principais soluções estão os dispositivos de segurança, que são projetados para prevenir acidentes e minimizar riscos durante a operação.
Entre os dispositivos de segurança mais comuns estão os interrompedores de emergência, que permitem parar o funcionamento da máquina imediatamente em caso de situações de risco. Esses dispositivos devem ser facilmente acessíveis e visíveis para todos os operadores, garantindo uma resposta rápida quando necessário.
As proteções móveis e fixas também desempenham um papel crucial na segurança. As proteções móveis permitem acesso seguro às partes da máquina que requerem intervenção, enquanto as fixas são projetadas para evitar que o operador entre em contato com componentes perigosos durante a operação.
A automação de dispositivos de bloqueio e segurança, como cortinas de luz e sensores de proximidade, é outra prática eficaz. Esses dispositivos detectam a presença de pessoas ou objetos em áreas perigosas e interrompem o funcionamento da máquina automaticamente, evitando acidentes.
A sinalização de segurança é igualmente vital para alertar os colaboradores sobre riscos potenciais. As placas e avisos devem ser claras e visíveis, informando sobre os procedimentos seguros e os perigos associados ao manuseio de máquinas. Uma boa sinalização ajuda a aumentar a conscientização dos trabalhadores e a promover um comportamento mais seguro.
Além disso, a combinação de treinamento regular e atualização das sinalizações assegura que os colaboradores estejam sempre cientes das melhores práticas de segurança e dos novos riscos que possam surgir. A educação contínua é um elemento chave para a eficácia das soluções de proteção.
Treinamento de colaboradores sobre segurança em máquinas
O treinamento de colaboradores sobre segurança em máquinas é uma etapa essencial para garantir um ambiente de trabalho seguro e eficiente. A capacitação adequada não apenas prepara os operadores para o manuseio seguro de equipamentos, mas também é uma exigência das normas de segurança.
Um programa de treinamento eficaz deve abordar as principais normas de segurança, os riscos associados às máquinas e as práticas adequadas de operação. É importante que o conteúdo do treinamento seja adaptado ao tipo de máquinas com as quais os colaboradores irão trabalhar, levando em consideração as especificidades e os potenciais perigos.
As sessões de treinamento devem incluir tanto a teoria quanto a prática. Os colaboradores precisam entender como as máquinas funcionam, quais são os seus sistemas de segurança, e qual é o procedimento de emergência em caso de falhas. Demonstrações práticas e simulações de situações de risco ajudam a solidificar o aprendizado.
Além disso, a realização de treinamentos regulares é imprescindível. Máquinas e processos podem evoluir com o tempo, assim como as normas de segurança. Atualizações constantes no treinamento garantem que os colaboradores estejam cientes de novos riscos e procedimentos, promovendo um ambiente de trabalho em constante melhoria.
A cultura de segurança deve ser incentivada dentro da empresa. Isso pode ser feito promovendo diálogos abertos sobre segurança, onde os colaboradores se sintam à vontade para relatar preocupações e sugestões. Iniciativas como campanhas de conscientização e workshops também contribuem para fortalecer essa cultura.
Por fim, a avaliação da eficácia do treinamento é fundamental. Realizar testes e questionários após as sessões ajuda a verificar a compreensão dos colaboradores e a identificar áreas que precisam de mais atenção. Investir no desenvolvimento contínuo das habilidades dos colaboradores é um dos principais caminhos para garantir a segurança no ambiente industrial.
Manutenção preventiva como parte da proteção de equipamentos
A manutenção preventiva é uma prática essencial na proteção de equipamentos industriais, pois garante que as máquinas operem de forma eficiente e segura ao longo do tempo. Esse tipo de manutenção envolve inspeções regulares e ações corretivas realizadas antes que ocorram falhas, evitando paradas inesperadas na produção.
Entre os principais benefícios da manutenção preventiva, destaca-se a identificação precoce de problemas potenciais. Realizar inspeções programadas permite que os operadores detectem desgastes, folgas e outras irregularidades que podem aumentar o risco de acidentes ou falhas operacionais. Isso não apenas assegura a segurança dos colaboradores, mas também prolonga a vida útil do equipamento.
Além disso, a manutenção preventiva contribui para a redução de custos. Ao evitar falhas graves, as empresas podem evitar gastos com reparos emergenciais e substituição de peças danificadas. A manutenção regular ajuda a manter os equipamentos em condições ideais, resultando em uma operação mais confiável e econômica.
Outro aspecto importante é o cumprimento de normas de segurança, como a NR-12, que exige que as máquinas sejam mantidas em boas condições de funcionamento. A manutenção preventiva é uma forma de garantir que os requisitos de segurança sejam atendidos, protegendo os colaboradores e a empresa de possíveis penalidades legais.
A implementação de um cronograma de manutenção preventiva deve ser baseada nas recomendações do fabricante e nas condições de operação das máquinas. Fatores como a frequência de uso, as condições ambientais e a complexidade da máquina influenciam a periodicidade das manutenções. Documentar as atividades realizadas também é fundamental para manter um histórico que facilite futuras análises.
Por último, a conscientização e o treinamento dos colaboradores sobre a importância da manutenção preventiva é essencial. Garantir que todos os envolvidos entendam a necessidade de seguir o cronograma de manutenção ajuda a criar uma cultura de segurança e cuidado, resultando em um ambiente de trabalho mais seguro e produtivo.
Estudos de caso: empresas que se destacaram na proteção de máquinas
Estudos de caso de empresas que se destacaram na proteção de máquinas oferecem insights valiosos sobre as melhores práticas de segurança. Um exemplo notável é a empresa XYZ Indústria, que implementou um conjunto abrangente de medidas de segurança para seus equipamentos, resultando em uma redução significativa de acidentes de trabalho nos últimos anos.
A XYZ Indústria investiu em dispositivos de segurança, como cortinas de luz e paradas de emergência, além de realizar treinamentos regulares com seus colaboradores. Essa abordagem proativa culminou em um ambiente de trabalho mais seguro e em uma melhoria da produtividade, pois as interrupções devido a acidentes diminuíram consideravelmente.
Outro caso de sucesso é a empresa ABC Metalúrgica, que focou na manutenção preventiva como parte de sua estratégia de segurança. Ao adotar um cronograma rigoroso de inspeções e manutenções programadas, a ABC Metalúrgica conseguiu identificar e corrigir problemas antes que se tornassem sérios, garantindo não apenas a segurança de seus operadores, mas também mantendo a produção sem interrupções.
A ABC Metalúrgica também promovia uma forte cultura de segurança dentro da empresa, incentivando os colaboradores a relatar preocupações e participar ativamente no desenvolvimento de novas práticas de segurança. Isso criou um ambiente onde todos se sentiam responsáveis pela segurança, resultando em um impacto positivo na moral e eficiência da equipe.
Por fim, a DEF Fabricação, uma grande empresa do setor automotivo, implementou tecnologias inovadoras de automação e classificação de segurança em seus processos. Ao usar sensores avançados e sistemas de monitoração, a DEF Fabricação foi capaz de otimizar suas operações, minimizando riscos e melhorando a segurança. Essa integração tecnológica não só fez a empresa se destacar em termos de proteção de máquinas, mas também a posicionou como líder no mercado.
Esses estudos de caso demonstram que a proteção de máquinas não é apenas uma obrigação legal, mas uma estratégia eficaz que pode levar à melhora significativa na segurança dos colaboradores e na eficiência operacional. Cada uma dessas empresas ilustra como a combinação de dispositivos de segurança, manutenção preventiva e treinamento contínuo resulta em ambientes de trabalho mais seguros e produtivos.
A proteção de máquinas e equipamentos é um aspecto fundamental para garantir a segurança no ambiente industrial. Ao adotar práticas eficazes, como o cumprimento de normas de segurança, a implementação de dispositivos de proteção e a realização de treinamentos regulares, as empresas podem criar um ambiente de trabalho mais seguro.
Além disso, a manutenção preventiva se mostra essencial não apenas para prolongar a vida útil dos equipamentos, mas também para prevenir acidentes e melhorar a eficiência operacional. Casos de empresas que se destacaram nesse aspecto demonstram que a segurança deve estar no centro das operações industriais.
Portanto, investir em proteção de máquinas não representa apenas uma necessidade legal, mas também uma estratégia inteligente para promover a saúde e o bem-estar dos colaboradores, bem como para garantir a continuidade e a qualidade da produção. O compromisso com a segurança deve ser um valor central em cada organização, assegurando que todos possam trabalhar em um ambiente protegido e eficiente.